Understanding Custom CNC Parts Suppliers: Revolutionizing Metal Fabrication
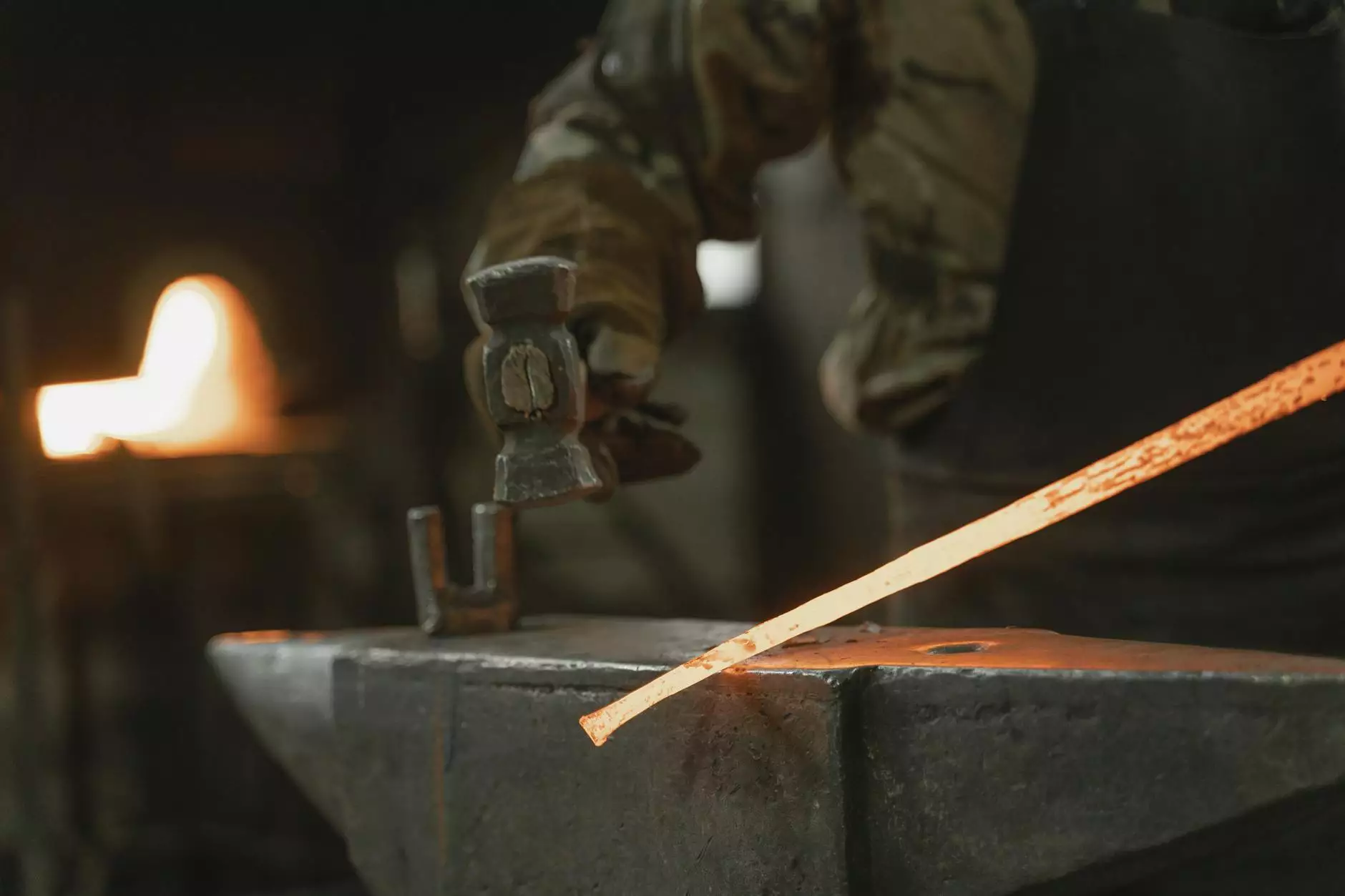
In today's competitive manufacturing environment, custom CNC parts suppliers play a pivotal role in ensuring quality, precision, and efficiency in the production process. As businesses increasingly rely on advanced technologies, the demand for high-quality CNC machined parts continues to rise. This article dives deep into the world of custom CNC parts suppliers, exploring their significance, benefits, and the key factors to consider when choosing the right supplier for your needs.
The Role of Custom CNC Parts Suppliers in Metal Fabrication
CNC, or Computer Numerical Control, is a technology used to control machine tools through a computer. The automation of machine tools results in exceptionally high precision, allowing manufacturers to produce complex geometries that would be difficult or impossible to achieve through manual machining. Custom CNC parts suppliers specialize in this technology, providing tailored solutions that meet specific customer requirements.
What Are Custom CNC Parts?
Custom CNC parts are components that manufacturers design and fabricate according to specific specifications. Unlike standard parts, which are mass-produced, custom parts are made with unique features and dimensions to meet the distinct needs of a business or project. This custom approach ensures that the parts are not only functional but also align perfectly with the overall design of the system they serve.
Benefits of Working with Custom CNC Parts Suppliers
Choosing to partner with reputable custom CNC parts suppliers comes with a multitude of benefits:
- Enhanced Precision: CNC technology offers unparalleled accuracy, which is crucial in industries such as aerospace, automotive, and medical devices.
- Tailored Solutions: Suppliers can create unique parts that meet the exact specifications required for your project.
- Cost-Efficiency: While custom parts may have a higher initial cost, they often result in long-term savings by reducing waste and increasing the lifespan of the components.
- Versatility: A wide range of materials can be used in CNC machining, including metals, plastics, and composites.
The Custom CNC Parts Manufacturing Process
The manufacturing process of custom CNC parts involves several critical steps:
- Design: Using CAD (Computer-Aided Design) software, engineers create detailed designs for the parts.
- Programming: The designs are then translated into code that guides the CNC machine's movements.
- Machining: The CNC machine cuts, shapes, and finishes the material as per the programmed instructions.
- Quality Control: Each part undergoes rigorous inspection to ensure it meets the required specifications.
Factors to Consider When Choosing Custom CNC Parts Suppliers
When selecting a custom CNC parts supplier, it is essential to consider several factors that affect the quality of service and the end product:
1. Expertise and Experience
Look for suppliers who have a proven track record in the industry. Experienced manufacturers are more likely to understand the intricacies of various materials and production techniques, allowing them to deliver higher quality products.
2. Technology and Equipment
Advanced and well-maintained machinery is critical to achieving precision. Suppliers should utilize state-of-the-art CNC machines and software to ensure top-quality outputs.
3. Material Options
Select suppliers that offer a wide variety of materials, including different grades of metals and plastics. The more options available, the better you can customize parts to fit your specific needs.
4. Quality Assurance Processes
A robust quality assurance system ensures that all parts meet industry standards and customer expectations. Inquire about the supplier's inspection methods and certifications.
5. Customer Support
Responsive and knowledgeable customer service can greatly impact your experience. Choose suppliers who prioritize communication and can address your concerns promptly.
Industries That Benefit from Custom CNC Parts
Numerous industries benefit from the precision and customization that custom CNC parts suppliers provide. Here are some key sectors:
- Aerospace: Parts must meet strict safety and performance standards.
- Automotive: Custom components contribute to vehicle efficiency and safety.
- Medical Devices: Precision is crucial for components that operate in sensitive environments.
- Electronics: Custom parts can enhance device performance and reliability.
- Heavy Machinery: Durable and custom parts are essential for operational efficiency.
Quality Assurance in Custom CNC Machining
Quality assurance is a non-negotiable aspect when dealing with custom CNC parts suppliers. Quality assurance involves a series of processes and techniques to ensure that the manufactured parts meet the required specifications. Here are the main components of quality assurance:
1. Material Inspection
Before production, raw materials should be inspected for quality, composition, and compliance with specifications. This step is crucial to prevent defects in the final product.
2. In-Process Inspection
Continuous monitoring during the machining process helps catch any issues early on. This can involve regular measurements and assessments to ensure that dimensions remain within tolerance.
3. Final Validation
Once the parts are manufactured, they should undergo a final inspection to confirm that they meet the required standards. This includes dimensional checks and functional testing where applicable.
4. Documentation and Control
Good suppliers will maintain thorough documentation of the production process, including material certifications and inspection records. This traceability is important for any future quality checks and audits.
Conclusion: Partnering with the Right Custom CNC Parts Suppliers
In summary, partnering with reliable custom CNC parts suppliers is essential for businesses looking to enhance their manufacturing processes. By ensuring precision, customization, and quality, these suppliers can contribute significantly to your project's success. When selecting a supplier, consider their expertise, technology, and quality assurance processes to align with your specific needs.
With the right supplier, your business can achieve remarkable results through customized precision components, leading to improved product quality and increased operational efficiency. Selecting the perfect custom CNC partner can set your business apart in a competitive marketplace, driving innovation and delivering unmatched value to your customers.